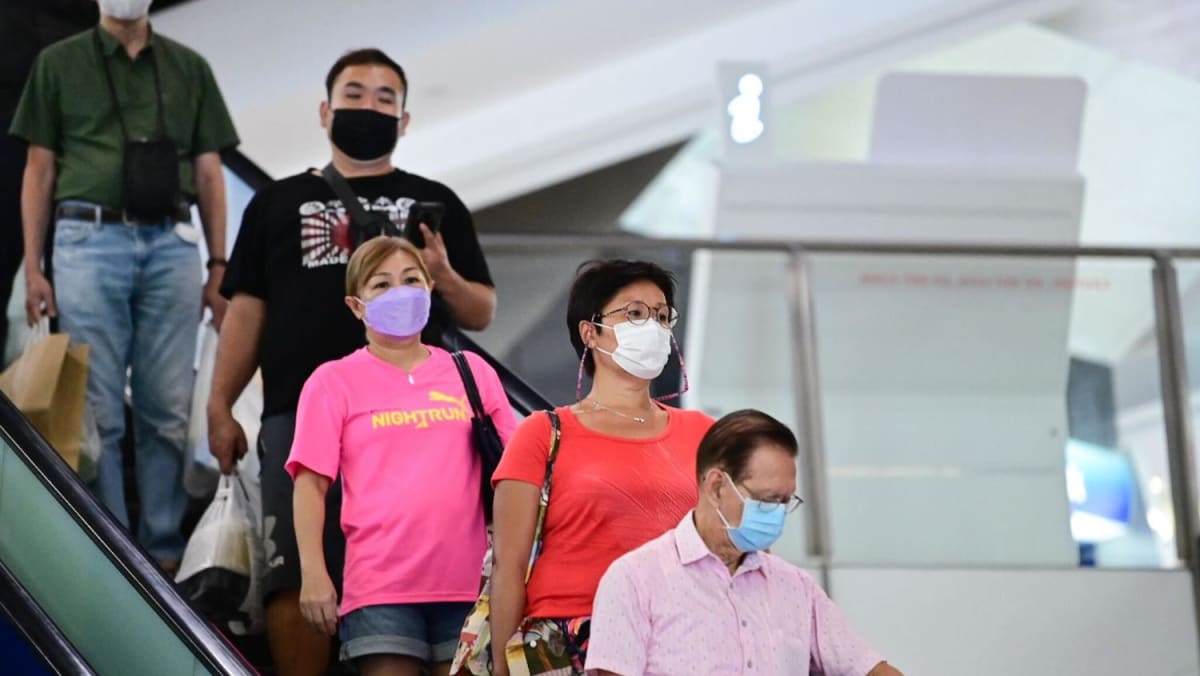
Technology company Razer told CNA it will be slowing down its face mask production following the easing of mask restrictions.
Razer said it started making masks during the peak of the COVID-19 pandemic due to the global shortage, and “converted existing product manufacturing lines to make and donate face masks for immediate relief”. The company also started Singapore’s first fully automated mask production and packing line.
SCALING BACK PRODUCTION
Some companies had already scaled back production when mask requirements outdoors were lifted earlier this year.
Director of AVS Technologies Kelvin Mun told CNA that the company already stopped production of face masks earlier this year, and fully shut down its mask manufacturing line in June.
Everything lined up, he said, adding that the company’s raw materials for mask manufacturing were used up at around the same time it was due to renew its mask manufacturing licence with the Health Sciences Authority.
The company, which sells printing equipment, set up its mask manufacturing line in March 2020 at the start of the COVID-19 pandemic because it could not buy enough masks for its own use.
“We saw that there was a short supply and everyone was panicking and they needed the masks. We thought that we could fill the gap to help supply the shortage,” Mr Mun said.
“It was a totally different thing (from our original business). It was difficult for us because we had to learn the new lingo from the medical side, all the requirements and paperwork that we were not used to.”
AVS Technologies sold its masks online and in army supplies shops, selling more than S$100,000 worth of masks per month at the peak of its production.
The company has managed to sell off most of its stock, with just a few cartons of kids masks remaining. It plans to donate the masks or share the masks with staff who have children.
Managing director of 3P Medical Device Joseph Ong also said his company had scaled back production by about 40 per cent over the past six months. The company also started producing masks in the first quarter of 2020, on top of Mr Ong’s other businesses.
The company used to produce about 300,000 to 400,000 masks per month, and produces about 200,000 now. It currently has no plans to scale operations down further, as 40 per cent of its customer base is still made up of corporate customers.
It also sells its masks with traditional Chinese medicine shops, hospital pharmacies, mom-and-pop stores, as well as online resellers like Shopee and Lazada.
“That was probably (because we were) anticipating when masks are no longer needed outdoors, there would come one day that the Government might announce that masks are no longer needed indoors,” he told CNA.
“But generally, after two-and-a-half years, the public has two sides, or preferences. One side, they prefer not to wear. The other side, they will still continue to wear,” he said, adding that many people still do not feel comfortable going around without a mask.
Singapore Technologies Engineering, or ST Engineering also began domestic production of medical-grade surgical masks in mid-February 2020, and the masks were used in Singapore’s hospitals on the frontline against COVID-19.
At the time, Singapore had to restart its domestic production capabilities when one of its foreign suppliers could not fulfill its contractual obligations recently to produce surgical masks, then-Trade and Industry Minister Chan Chun Sing said.
“Our medical-grade surgical mask business was set up with a clear objective, that is to help Singapore establish local mask manufacturing capabilities and strengthen mask supply chain resilience,” said ST Engineering.
In response to queries about whether the company would be stepping down mask production, ST Engineering said: “Our focus has always been on building a sustainable supply of medical-grade surgical masks and N95 masks for our healthcare and frontline workers, as well as local communities in need, and will remain so going forward.
“We have resilient capacity utilisation and business models which well address demand pattern changes.”
Meanwhile, Vital Shield told CNA it plans to maintain mask production or even scale up production if it secures more corporate clients.
The company started manufacturing masks at the start of the COVID-19 pandemic, adjacent to another cleaning company run by the team.
The manufacturer initially saw demand for masks drop by about 10 per cent when the outdoor restrictions were first relaxed. But demand gradually clawed back as Singapore saw infection waves from different variants of COVID-19 and monkeypox, said its sales and marketing manager Mellissa Hau.
The company sells its masks on its website as well as on Shopee and Lazada. But since corporate orders make up about 65 per cent of its demand, the team plans to continue its current level of production. Many of its corporate clients are from industries that still require employees to wear masks, like in F&B or hospitality, said Ms Hau.
“We felt that masks were very expensive and their quality was not there. So we decided to do our own,” she added.
“The first year, business was good because that was the start, and people were trying to find affordable and quality masks. After about one-and-a-half years, more competition came in, especially from overseas where the cost was very low … so we got affected a little.”
This year, several players decided to shut down operations and focus on their other business, said Ms Hau.
“So the pie is bigger. Our share of the pie increases because some of the players have withdrawn from this industry.”