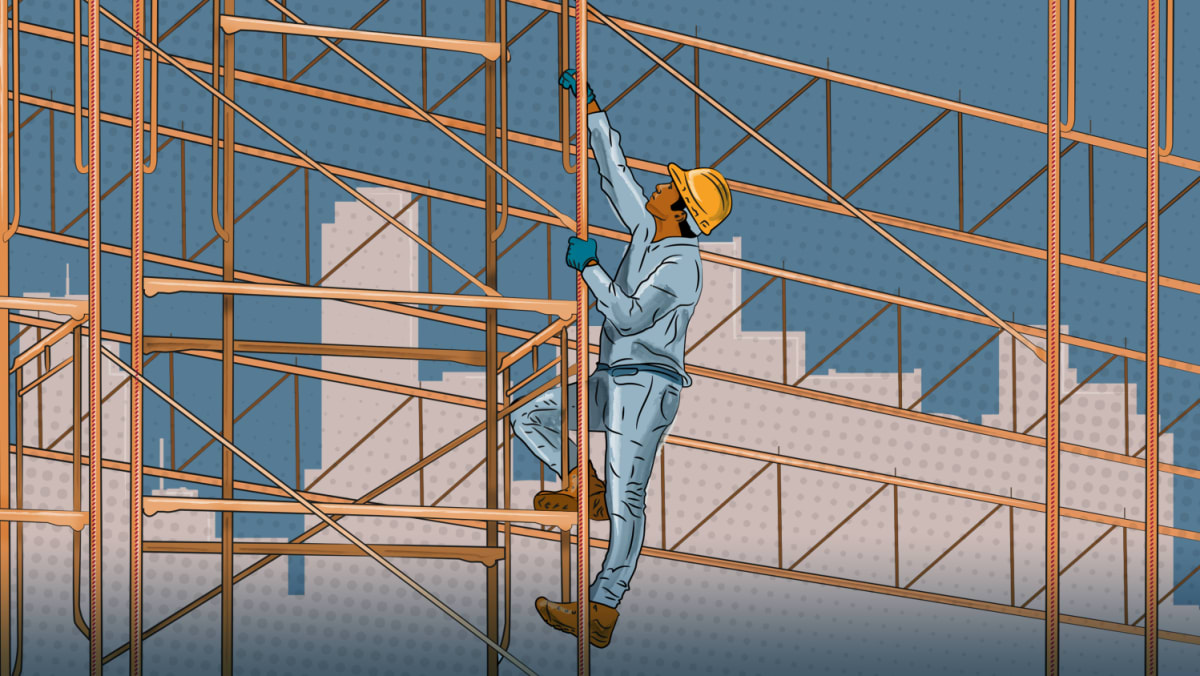
Mustafa returned to Bangladesh for a break right before the COVID-19 pandemic, then for two many years, he couldn’t return to Singapore to work because there were border restrictions.
Getting run out of money, he or she wanted to come to Singapore as quickly as possible and used any job which was available. He furthermore paid more than S$4, 000 in recruitment fees just to come here and function.
He stated that if he had documented his employer, he’d have been sent back home. “I have a lot of cash I loan, when I go back, the cash how do I pay? ” he asked. Great that he has hurt his leg, he might not be able to do hard labour in any way in the future.
Mister Luke Tan, situation manager at the Humanitarian Organisation for Immigration Economics (HOME), declared that employers hold lots of power over migrant workers because the recruitment costs are higher and the workers go into debt to work here.
“The more costs they incur, the more fear they will have, ” he or she said.
Mister Tan said that several companies took on too many projects or tried to cut costs simply by hiring too few employees and skimping on safety measures even before COVID-19. He feels that it should cost the companies more to break safety regulations, since human lives are on the line.
“We hope that instead of several administrative punishments, the particular authorities could think about more severe, stern activities for employers who are found to be not complying with protection rules. ”
SAVING COSTS, LACK OF EQUIPMENT
Comparable to what Mustafa referred to, at times, the workers want to be safe but don’t have the resources to do so.
Office safety experts CNA talked to said that safety starts through the planning and budgeting stage, and sometimes, it’s too late by the time inspections come around.
Experienced basic safety consultant Han Wenqi said that in his many years in the industry, he has often come across situations where managers and administrators tell him that the creator never budgeted for your safety precautions this individual thinks are necessary.
There are times when workers are wearing safety makes use of, but these are not linked to a lifeline, or maybe the lifelines are hooked to a point that will won’t support the particular worker’s weight. The particular workers are still at risk of falling “just by having an extra full-body harness”, he said, adding that this “goes back to time and money”.
Not only could be the safety equipment costly, anchor points for your lifelines should be set up by professional technical engineers after making the required calculations, he mentioned. But some work websites skip this step.
“They will manage the expenditure by forgoing the safety provision or not even having a safety provision, ” he mentioned. He thinks this is linked to how projects are often awarded to the lowest bidder.