China is a leading aluminium producer and consumer but it lacks the high-quality ore needed to make it. The country otherwise relies on imported metal ore from Guinea and Australia– but that could quickly change.
A flower in the northern province of Shanxi is being upgraded with a French technologies that will allow it to develop metal from China ’s low-grade metal that was formerly inoperable.
The Bayer approach, invented by Austrian scientist Karl Josef Bayer in 1888, is commonly used to enhance ore into smelting-grade oxide, or metal oxides – the forerunner to aluminium.
Do you have concerns about the biggest issues and changes from around the globe? Find the answers with SCMP Knowledge, our innovative platform of customized content with explanations, FAQs, assessments and infographics brought to you by our award-winning group.
But it is not an effective or cost-effective approach to develop ore with a high sand articles, the main metal type in China. Silica is an contamination that could result in a significant reduction of aluminium and caustic soda – a answer used to break bauxite in the Bayer procedure.
After a century of research, French chemist Jean Ocello, from clean tech firm IB2, has come up with a way to transform low-grade ore into a high-quality materials. The procedure neutralises silica and sulfur, meaning high-silica ore may be refined using the Bayer technique.
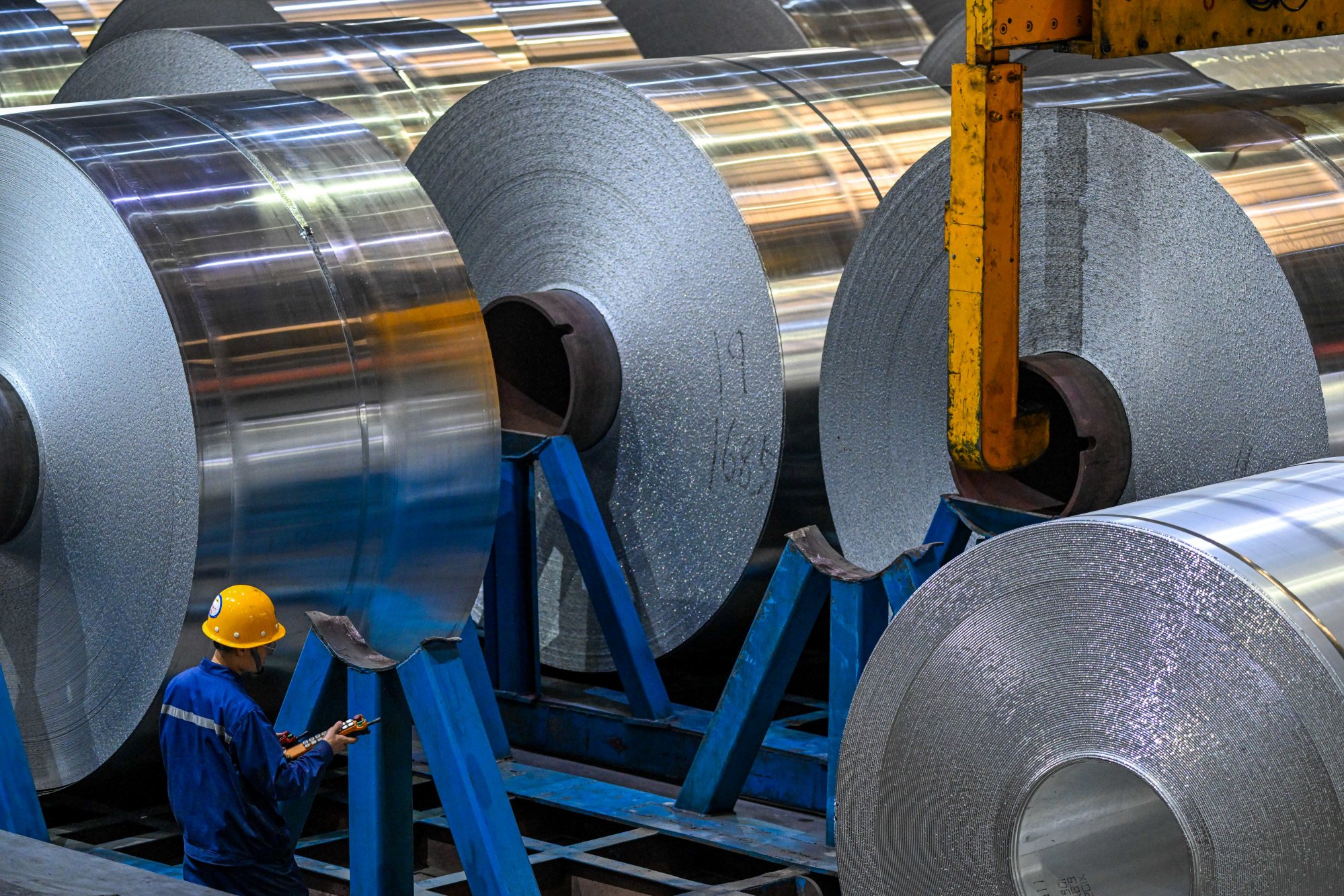
In 2023, IB2 signed a 22-year deal with Taiwanese strong Liulin Senze Coal & Aluminum to move over to the systems.
Under the bargain, IB2 engineers in Europe will track 60 parameters in the aluminium production process– including solvent dosing, thermal gradients and temperature control – at the plant in Shanxi province and recalibration will take place every three to six months to adapt to changes.
Romain Girbal, chief executive and co-founder of IB2, said the technology would enable Beijing to achieve its goal of reducing dependence on imported high-grade bauxite, to make use of domestic low-grade reserves and produce aluminium in a greener way.
“It is a direct enabler of China ’s strategy to own its inputs, control its compliance, and operate at scale without external veto points, ” he said.
“IB2 will allow China to rebalance its bauxite supply towards a more China-centred strategy, which is aligned with Asia looking for more commodity sovereignty in reaction to a more unsecured globalised trade market.
“Over time, we fully expect China ’s import reliance on Guinea and Australia to shift from dominance to minority. These suppliers will not vanish, but their bargaining power, price leverage and strategic centrality will diminish. ”
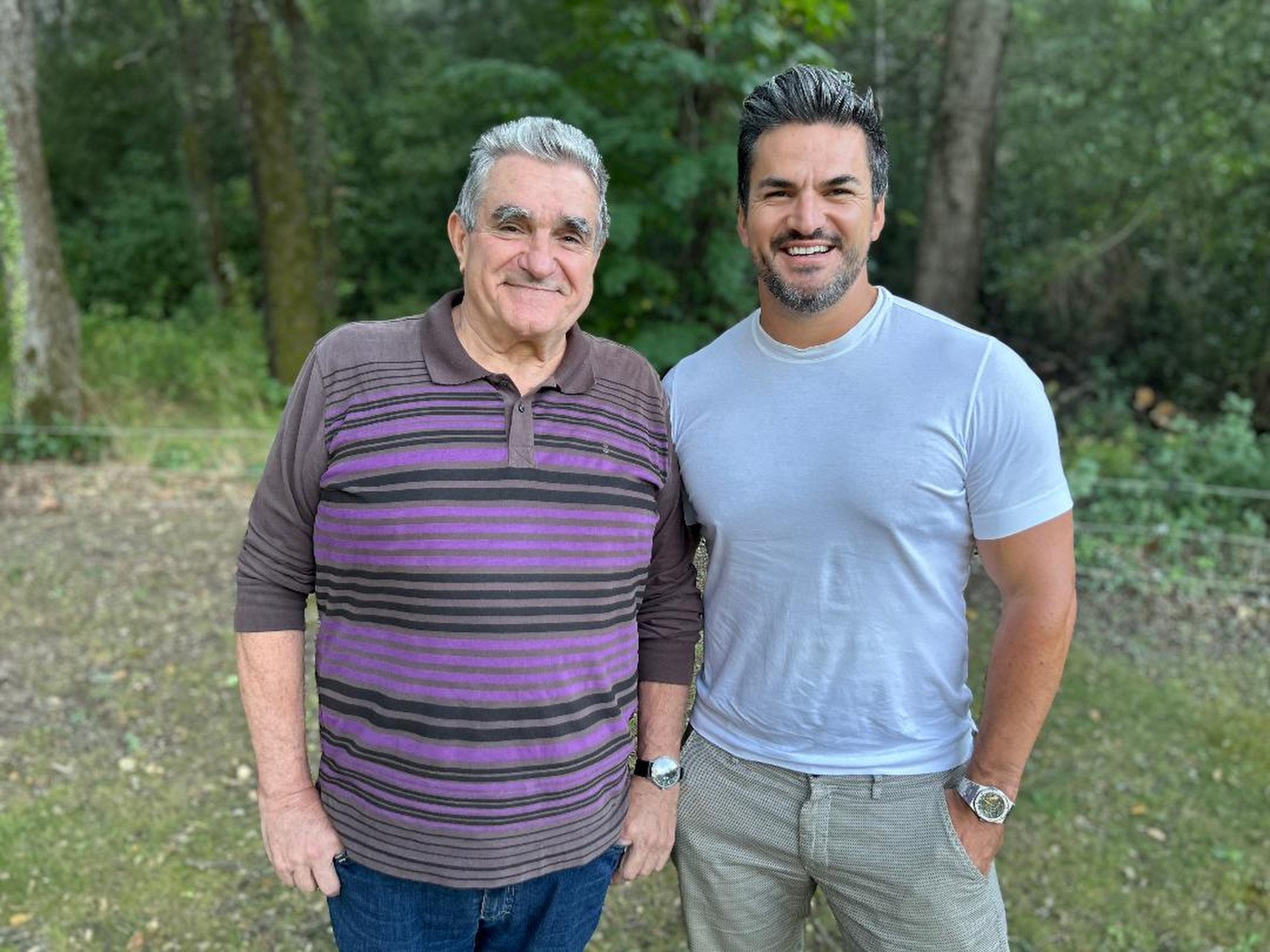
According to data visualisation platform Observatory of Economic Complexity, China ’s aluminium ore imports totalled US$ 10. 6 billion in 2024. Guinea was the largest supplier at US$ 7. 65 billion, followed by Australia at US$ 2. 31 billion and Turkey with US$ 187 million. Its exports were minimal at US$ 5. 9 million.
Australia has the world’s largest bauxite reserves. Its aluminium industry is a key employer in areas outside major Australian cities, providing 17,000 jobs, according to a 2021 report by industry group the Australian Aluminium Council.
It said that while alumina and aluminium ores (bauxite) were Australia’s fourth largest mineral export, the product aluminium was its highest earning manufacturing export.
Use of the lightweight industrial metal has seen relatively high growth globally, with wide applications in the vehicles, construction, transport and consumer packaging sectors such as windows, aircraft and beverage cans.
Liulin Senze Coal & Aluminum currently produces 1. 3 million tonnes of alumina a year, valued at 3 billion yuan ( US$ 412. 5 million ).
The Chinese firm supplies large state-owned enterprises such as Shaanxi Non-ferrous Metals Holding Group, China Aluminum International Trading Group and Jiuquan Iron and Steel Group.
Girbal said the first full-scale unit was 85 per cent complete by the end of April and would be operating at industrial scale from July, with full production expected for early 2026.
The first unit is designed to process 600,000 tonnes of low-grade bauxite annually. The second phase, which will increase annual capacity to 3 million tonnes, is about to enter the engineering stage.
“The beneficiation layer [separating valuable minerals from unwanted materials ] is installed upstream of digestion, delivering high-grade, low-impurity feed directly into conventional Bayer operations, ” Girbal said.
He said very low-grade bauxites had been purified there, exceeding the level in imported high-grade bauxites.
According to Girbal, the system reduces ore consumption by up to 30 per cent for every tonne of alumina produced.
“That means refineries can deliver the same output with significantly less bauxite, lower reagent loads and materially reduced environmental overhead– all without altering the core Bayer configuration, ” he said.
In the conventional process, around 4 tonnes of high-grade bauxite yield 2 tonnes of alumina, from which 1 tonne of aluminium is extracted by electrolysis.
Describing the technology as a “direct execution of state-enforced mandates”, Girbal pointed to Beijing’s two-year plan for the aluminium industry released in March.
The plan states that by 2027 “the resilience and security of the industrial chain and supply chain will be significantly improved”. It also says China will “strive to increase domestic bauxite resources by 3 to 5 per cent and the output of recycled aluminium by more than 15 million tonnes”.
It also calls for a greener industry by improving production technology, researching low-carbon smelting and precision processing technologies, and by using at least 30 per cent clean energy in aluminium production.
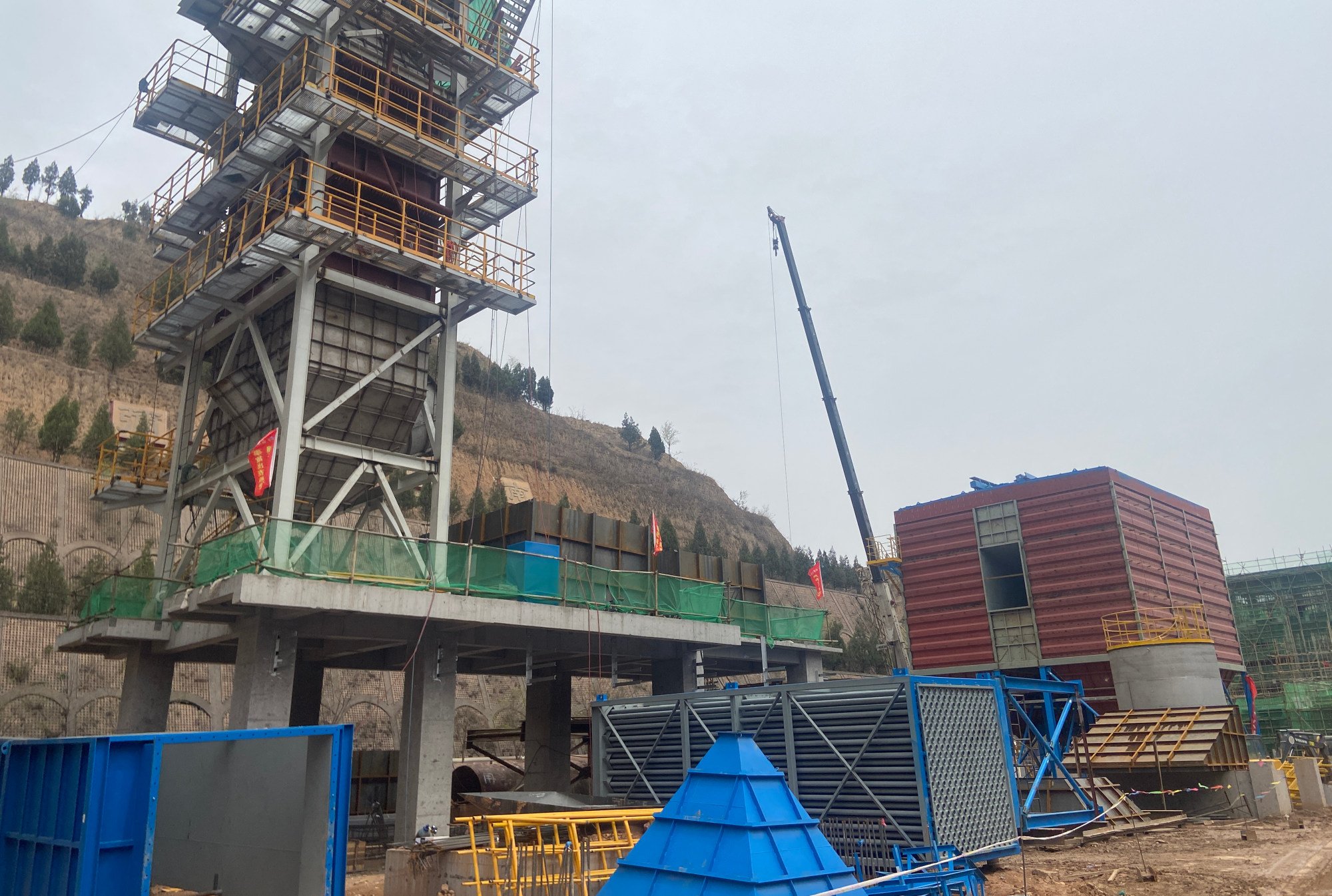
Girbal said his company ’s technology would help Chinese producers “increase yield, reduce reagent use and comply with domestic environmental, social and governance ( ESG) policy”, referring to Beijing’s directive.
He said refineries that relied on a blend of 60 per cent imported ore would be able to switch entirely to local supply, reduce operating costs and increase yield.
“As more refineries adopt IB2 the volume of imported high-grade bauxite will begin to reduce – not to zero, but enough to structurally rebalance the use of local Chinese bauxites versus imports, ” Girbal said.
Beyond China, he expected to see a rise in self-sufficiency in the aluminium market, adding that his company had identified India, Saudi Arabia, Kazakhstan and Turkey as potential clients.
He said bauxite sources in Central Asia were high in sulphur and silica, while the Middle East had stringent regulations on water and reagent consumption.
In India, the world’s second-largest aluminium producer, environmental pressures and land constraints pose challenges for the disposal of red mud, a toxic and alkaline by-product of aluminium production.
“ In each of these contexts, IB2 has already been validated or is under active engagement, ” he said.
“ When countries like China, India, Kazakhstan and Saudi Arabia can process domestic low-grade ore at parity or better – without importing, blending, or violating ESG norms – the leverage held by current exporters declines. Freight arbitrage shrinks, price premiums soften, dependency falls. ”
More from South China Morning Post:
For the latest news from the South China Morning Post download our mobile app. Copyright 2025.